British manufacturing benefits from Geely’s forward looking international thinking
“Holyhead Road was a hundred years old, jammed in between two motor dealerships. The wind used to lift the roof off and it used to rain on the inside” says Production Manager, Vehicle Assembly, Steve Fitter about LEVC’s original manufacturing facility in Coventry, part of the industrial heartland of the United Kingdom known as the Midlands.
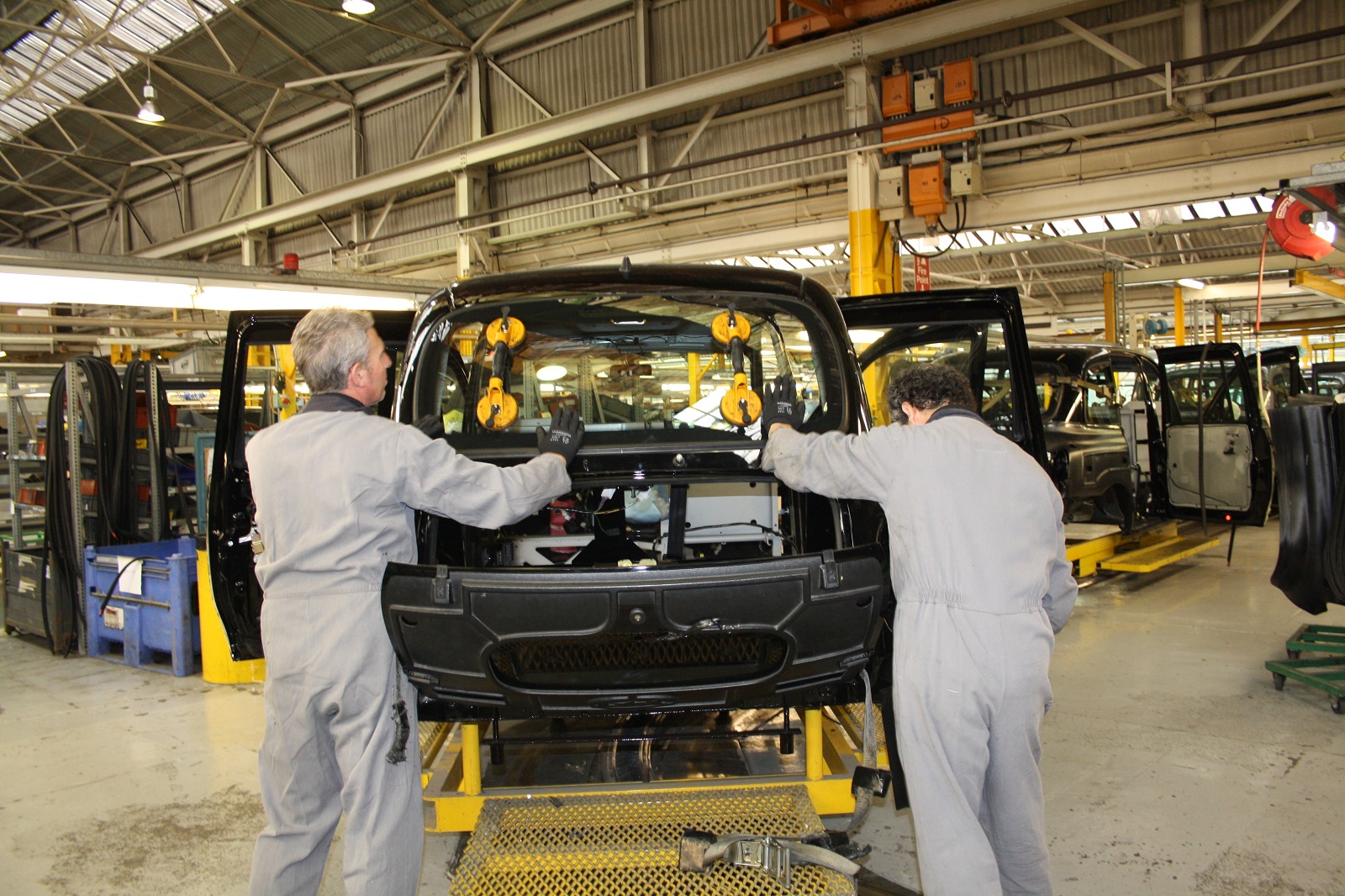
Old LTC Holyhead Road Plant
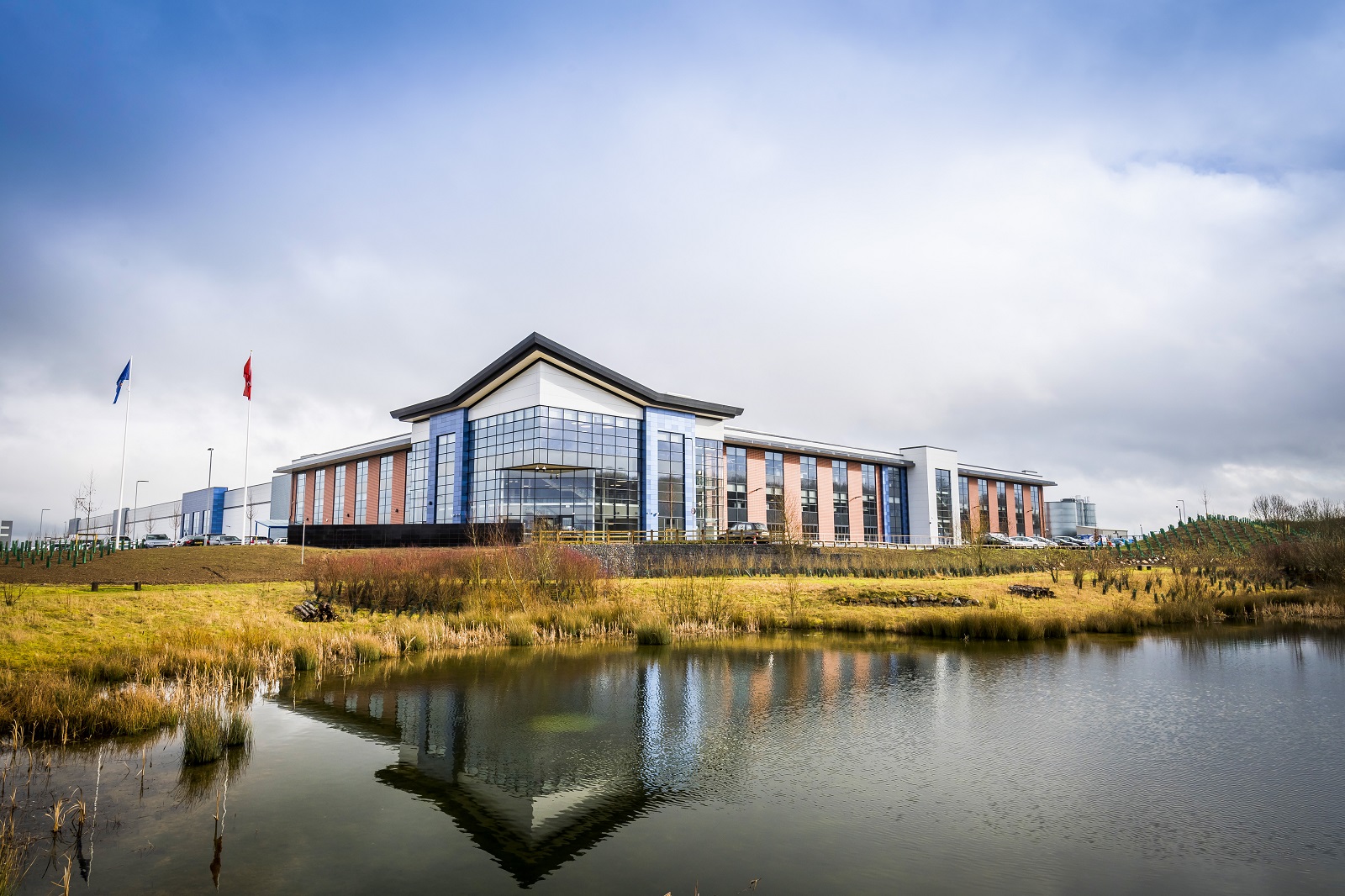
New LEVC HQ and Plant in Ansty
Geely’s investment in Coventry is a text book example of what Chinese companies can achieve when they get FDI right. A £325 million project it is the first newly built car production facility for over ten years in the UK and the first dedicated to the production of electric vehicles. Covering 37,000m² it houses both the production facilities of London Electric Vehicle Company (LEVC) – the successor to London Taxis International (LTI) – along with Emerald Automotive Design (EAD) and their respective offices. From September last year the LEVC TX a brand new taxi to meet the new environmental requirements of Transport for London along with the demands of 21st century passengers entered production.
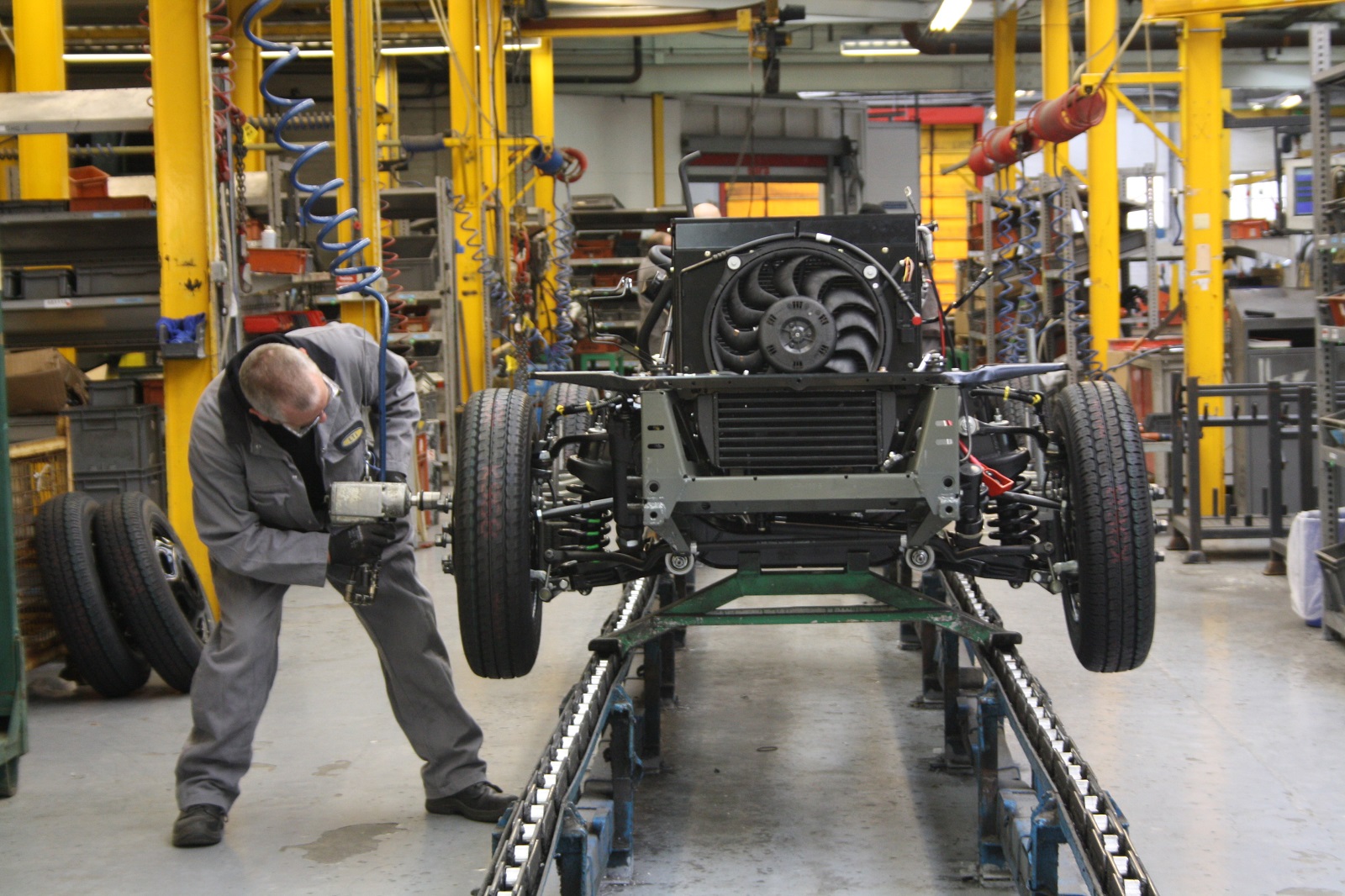
TX4 Assembly in Holyhead Road Plant
The factory floor of the state of the art facility shows how far removed the company is from its leaky roofed Holyhead Road days which for 70 years played host to manufacturing the London icon. Geely has been involved with its production since the forming of a joint venture with the company in 2007 which involved parts supply. After the company which e-coated the body for LTI went into receivership Geely stepped in making bodies for the old TX4 taxi and sending them from China to Coventry.
In a high tech dust free environment, separated from the rest of the factory by a glass wall, the body building process has been brought back to the UK. “Because there is no welding the whole body structure part is a controlled environment. You see the people in there are wearing white paper overalls, that is because there are two processes which are predominantly cleanliness critical. There is hot-cure and cold-cure which are gluing processes” explains Steve.
With the new TX taxi most of the anodised aluminium structure is joined together by adhesive. In the case of hot-cure the parts are essentially assembled glued and riveted and then baked in an oven to set the adhesive. After baking the body, more parts can be added on with cold-cure adhesive.
Once the shell emerges from the body shop overhead carriers pick it up and the more traditional assembly line begins. At each stage, though, high-tech quality checking devices monitor the progress and ensure standards are met. Much of the production is done using direct current (DC) tooling. “It’s a quality control system that makes the operator complete the process to the required sequence with the correct tools and it will not allow the vehicle to move forward until it is done” explains Steve. The system uses WiFi and Bluetooth to communicate and computers show the operator the required work.
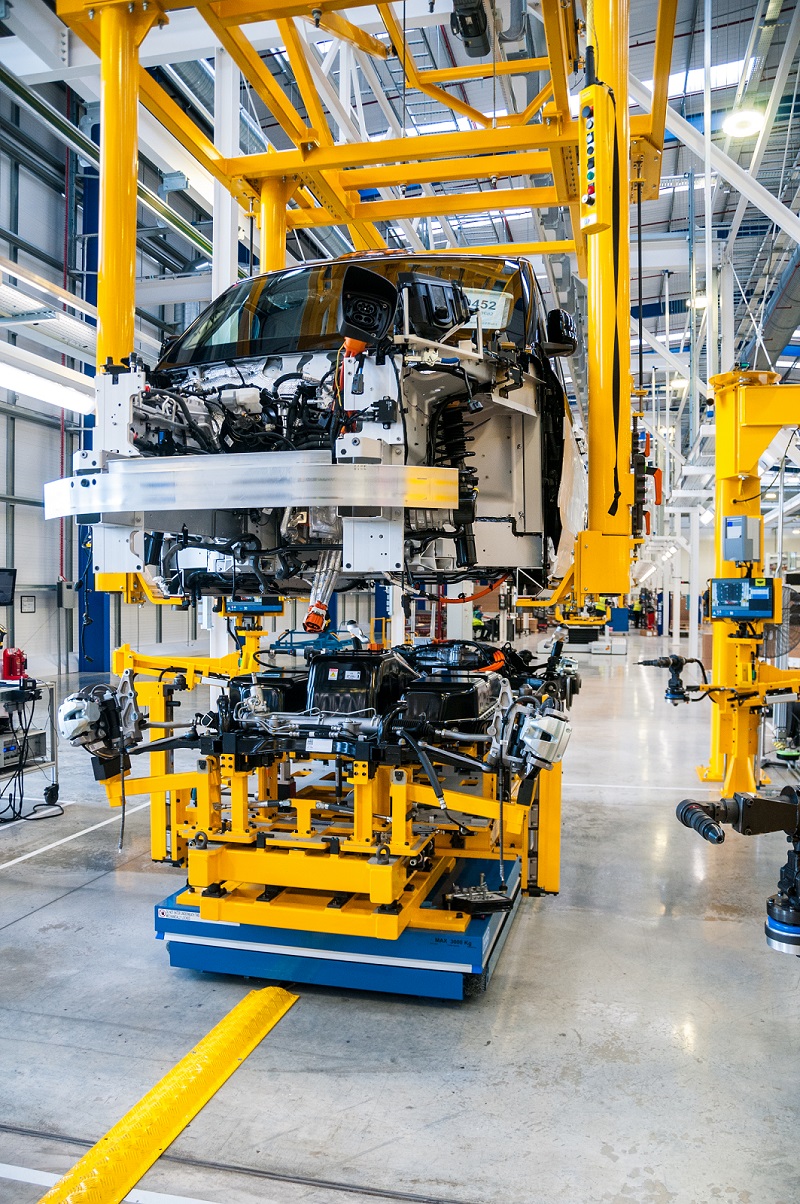
Anodised aluminium TX5 lowered onto chassis unit in new Anstry Plant
Surprisingly there is only one robot on the vehicle assembly line and that is for the glazing, the rest is all about the fourth industrial revolution – using the technology to assist the people on the production line to do the best possible job and take away the margin of error that they can make.
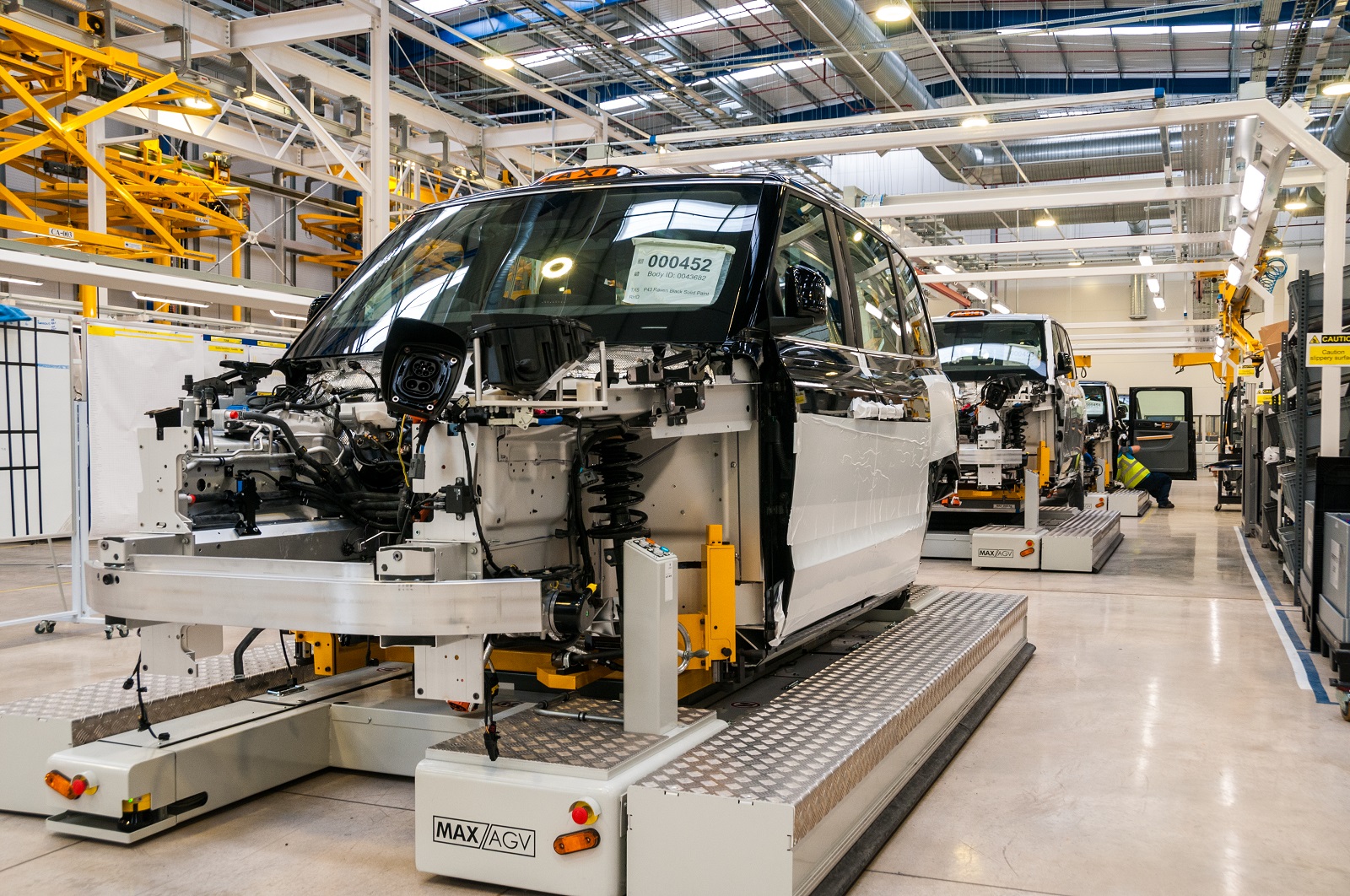
Automatic Guided Vehicles (AGV) ferrying semi-complete TX5 around Ansty Plant
After installing various electrical systems the bodies transfer to automatic guided vehicles (AGV) which then ferry them around the various fitting stations. One of the big advantages of this over a more traditional fixed assembly line is that it makes changes to the process much easier to implement and also to account for different body structures. Although currently the factory only produces the TX taxi, a van will soon be added to the production line as LEVC spearheads Geely’s electric commercial vehicle push.
With the tooling and support machinery also being electric it is a much quieter and far more people centric production environment than many traditional car plants. One of the last items to go onto the body is the doors so as to create unhindered access to the interior for operators.
Coming quite late in the process the body is mated to the chassis unit which includes the electric motor, battery, and kinetic energy regeneration system. This is a critical stage due to wheel alignment requirements. One of the last things to happen after adding the wheels and front module is the software download which then checks all the vehicles systems. The final thing to happen is the taxi’s first charge where it is plugged into a high voltage supply to allow it to drive its own way off the line.
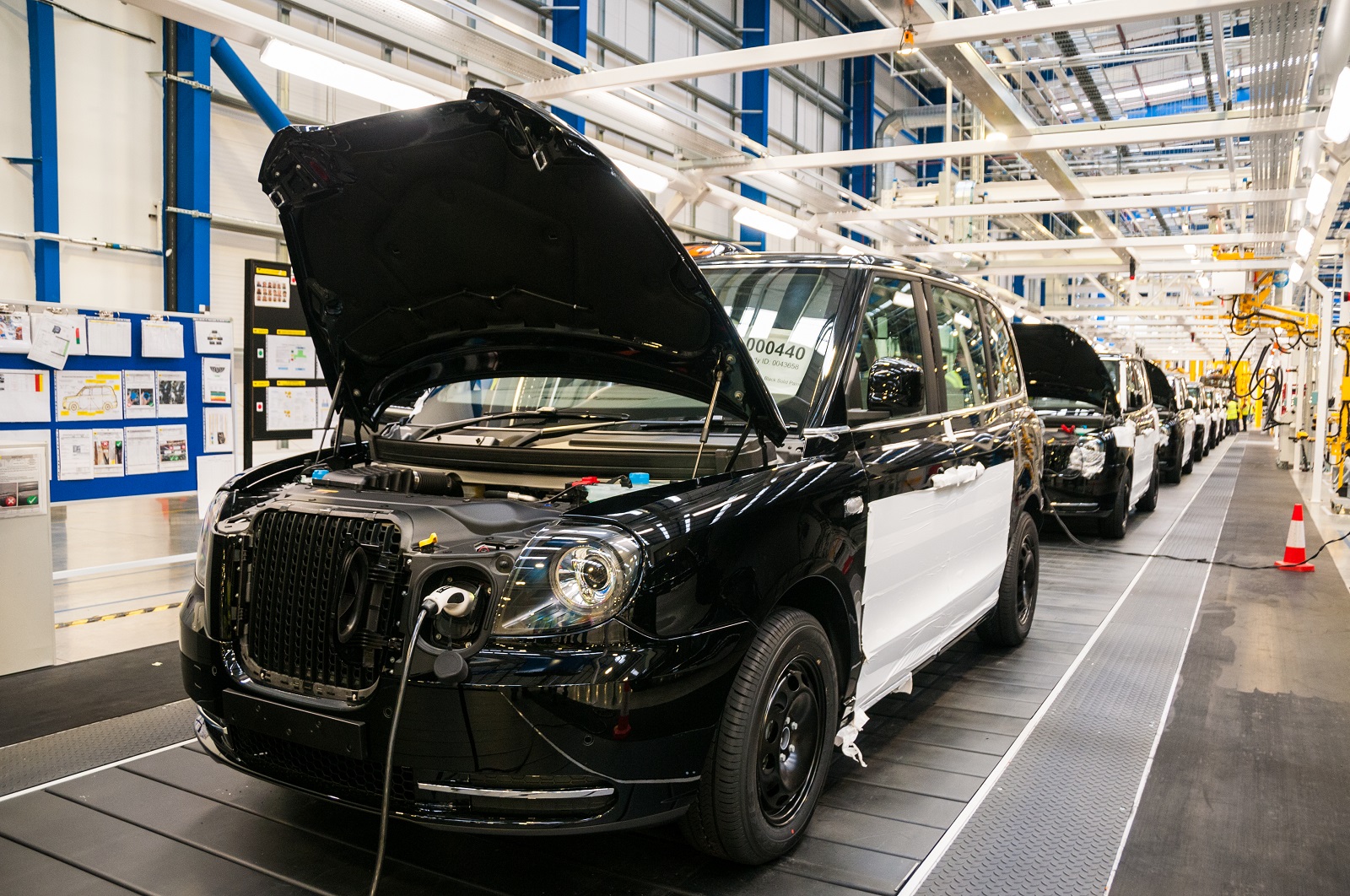
Finished TX5 receiving its first charge
The factory though doesn’t just produce green vehicles but is a green building itself. It achieved ‘excellent’ under the BREEAM rating which looks at certifying the sustainability of buildings. This along with the UK government A rating is thanks to features such as the use of 850m² of solar panels for electricity and the harvesting of rain water and waste heat for use in the facilities.